Lepidottero cangiante che galleggia tra le onde di salmastre contingenze; quale albero ha ospitato la tua camera del cambiamento? Quale aroma, di stupenda infiorescenza, accompagnava le tue giornate in guisa di brucante essere peloso e variopinto, quasi totalmente ricoperto di peluria urticante? Bruco che percorre le distese della verdeggiante nutrizione. Bruco ovvero l’ottimo vampiro delle piante, anche quando di piante, tutto attorno, non parrebbe sopravviverne nessuna. Fin dove quei tozzi pseudopodi ti hanno trasportato, tra il fragore delle macchine al servizio dell’industria concepita dall’umanità insapore. Cotto in mezzo ad una pasta resa fluida e malleabile, grazie al calore di una stella che non possiede alcun nome. Ma brucia, arde ininterrottamente, finché l’addetto all’altro lato della macchina non grida: “Fermi, fermi tutti. Un insetto è entrato nell’imbuto!” parte esplicita […Potrebbe rovinare il parison.] Parte implicita. Ma che cos’è, in parole povere, l’oggetto da cui prende il nome tale iconico passaggio intermedio di un certo tipo di processazione dei materiali… Un lungo tubo, essenzialmente, ma anche largo, a ben vedere, per lo meno nell’accattivante sequenza alla testa dell’articolo che state leggendo. Il tipo di breve video, tra il ricco novero di Internet, che ha cominciato negli ultimi tempi a fare la sua comparsa nei canali Instagram o TikTok, accompagnato da un roboante ritmo musicale da discoteca. La via d’accesso, se vogliamo, all’effimera attenzione della gente, per un tempo abbastanza lungo da apprezzare l’ingannevolmente semplice serie di passaggi e l’oggetto finale che ne consegue: ad esempio uno scintillante, giallissimo, idrodinamico kayak. Del tipo pronto a solcare le onde, ogni qualvolta l’orologio settimanale dei giorni raggiunge l’ora metaforica del week-end. Parrebbe quasi un’arcana manovra in grado di plasmare la materia, ma non lo è. Poiché siamo dinnanzi, direi che è giunta l’ora di rivelarlo, all’avanzata e vetusta tecnica dell’ormai quasi secolare stampaggio per soffiaggio, sebbene la sua applicazione in campo nautico paia essere alquanto recente. Per lo meno, dal modo in cui taluni dei protagonisti delle varie dimostrazioni online agiscono apparentemente sorpresi dal peso del natante ultimato, lasciandolo cadere rovinosamente sul rigido suolo dell’opificio. Dopo tutto, come ben sapete, questo tipo di termoplastica è “praticamente indistruttibile” una volta che ha raggiunto la temperatura ambiente. E a patto che non sia coinvolta dalle fiamme vive come avviene in certi gravi casi ad un tutt’altro altro tipo di scafi letteralmente imbevuti di petrolio. Ma navi cisterna qui non prendono di certo forma, bensì piuttosto la versione navigabile del sostanziale approccio figlio di un bisogno molto rappresentativo dei tempi contemporanei: avere la cosa subito, perfettamente conforme, essenzialmente pronta all’uso fatta eccezione per il bisogno di tagliarne delicatamente i contorni inesatti. Soltanto per gettare la materia di troppo nuovamente nel magico calderone. Da cui possa, quasi subito, ridiventare un parison.
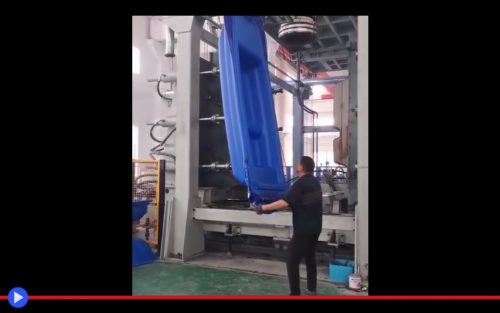
Ora l’utilizzo ripetuto ben due volte di un simile prestito linguistico dall’idioma francese (nell’accezione dell’antico verbo parer, fabbricare) è motivato dall’importanza che tale momento del ciclo produttivo riveste nella concezione stessa di una simile metodologia, introdotta per la prima volta negli Stati Uniti nel 1938 da parte di Enoch Ferngren e William Kopitke, che brevettarono a vendettero la prima macchina capace di realizzarne artificialmente uno alla Hartford Empire Company dell’Illinois. Tra le maggiori produttrici di bottiglie per il latte che venivano per lo più costruite, all’epoca, mediante l’utilizzo del vetro. Ed è proprio questo il punto interessante dell’intera faccenda poiché lo stampaggio per soffiaggio, originariamente, era la tecnica inventata per sostituire il soffio di un maestro vetraio, mediante la discesa meramente gravitazionale della sopradescritta “manica” ed il suo conseguente intrappolamento tra due metà di uno stampo, simili alle ante di una vergine di Norimberga. Poco prima che l’apposito ugello provveda ad inserire una copiosa quantità d’aria compressa all’interno dell’equazione, ottenendo un risultato che voi tutti, ritengo, potreste già esser prossimi ad intuire. Questo perché, per le prevedibili leggi della termodinamica, se una forza equivalente preme in ogni direzione contro le pareti di un involucro esterno, è del tutto naturale che la pasta (o gel) situato nell’intercapedine riesca a distribuirsi in modo pienamente conforme all’interno del profilo designato. Per poi diventare, al suo raffreddamento, l’essenza assai tangibile del pezzo originariamente pianificato. Dopo i primi timidi esperimenti con le resine polimeriche a base plastico, la svolta sarebbe quindi giunta all’inizio degli anni ’50, grazie all’introduzione sul mercato di un materiale come il polietilene ad alta densità (HDPE) perfetto per la creazione di oggetti leggeri e resistenti, perfettamente calibrati in base all’utilizzo finale. Soltanto al 1974, grazie all’inventore John Wesley Hyatt, risale anche l’introduzione dell’oggi altrettanto diffuso stampaggio ad iniezione, molto funzionale alla creazione di elementi in materiale plastico del tutto privi di una parte cava. Grazie all’immissione a forza in un diverso tipo stampo, tramite il foro d’uscita in quella che costituisce a tutti gli effetti una vite infinita incapsulata all’interno di un tubo, dove la materia prima (in genere dei pellet di termoplastica) viene squagliata tramite l’impiego dell’attrito e un apposito impianto di riscaldamento. Non che le due tecniche manchino di essere talvolta combinante, in ciò che in gergo viene definito injection blow molding (IBM) al fine di calibrare meglio l’immissione e la quantità di materiale utilizzato per ciascun pezzo finito.
Non che tale approccio entri nell’inquadratura nel caso della produzione dello fin qui mostrate barche o canoe, semplicemente perché su una tale scala i margini di tolleranza sono abbastanza ampi, da permettere la moderazione del flusso semplicemente mediante il blocco ad intervalli regolari dell’estrusore, mentre la naturale tendenza del parison a scendere si occuperà facilmente del resto. L’IBM è d’altra parte molto utile, e diffuso, nel caso della produzione delle bottiglie più piccole, dove il dosaggio attorno a un’anima precedentemente incorporata nello stampo risulta essere assolutamente determinante.
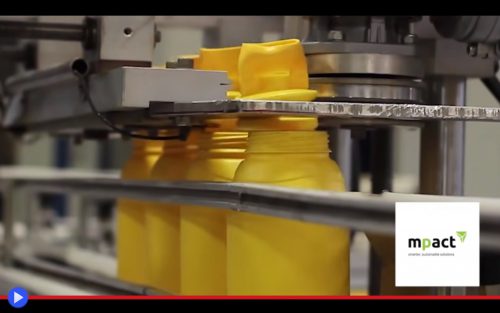
Come potrete facilmente immaginare, lo stampaggio a soffiaggio è una tecnica industriale che ha i suoi lati positivi e negativi, indissolubilmente pertinenti ad una qualsivoglia prassi di quel particolare campo d’intenti. Primo aspetto notevole la sua adattabilità a qualsiasi logica di scala, con la produzione rapida di grandi quantità di prodotto piccoli o grandi, ad un costo unitario (dopo l’approntamento del meccanismo) che risulta essere sorprendentemente irrisorio. Al punto che, nel costo finale al cliente, la maggior percentuale del mark-up deriva dalla questione logistica delle consegne e la necessità di ripagare l’alto costo per l’avvio iniziale della catena. Aspetto, quest’ultimo, accompagnato dalla problematica limitazione di dover sempre puntare ad un qualche tipo di oggetto cavo come risultanza finale del processo, a meno d’impiegarlo assieme a metodologie collaterali del sistema ad iniezione (con costi addizionali) oltre alla produzione di un’alta quantità di scarti. Poiché anche se la plastica risulta essere in linea di massima perfettamente riciclabile, non è sempre possibile farlo in maniera economicamente sostenibile. Soprattutto quando l’elasticità e plasmabilità della sua versione fluidificata risulti essere alla base del processo messo in pratica dall’azienda di turno.
Ogni filiera produttiva che si basa sul petrolio, d’altra parte, mostra ad oggi una fondamentale data di scadenza, nel momento stesso in cui le risorse sotterranee del nostro pianeta saranno prossime all’esaurimento. Ponendo finalmente al centro delle collettive disquisizione un qualche tipo di strada alternativa finalizzata alla realizzazione dell’oggetto desiderato. Anche dovessimo tornare al vetro, d’altra parte, non c’è verso che potremo liberarsi del sistema ereditato dal nostro piccolo amico metamorfizzante. Poiché da un sottovalutato bruco nasce sempre, ed ogni volta continuerà a farlo, la magnifica farfalla industriale delle circostanze. E lo stesso, a ben vedere, mai potrà cessare d’avvenire col suo simile creato dagli umani, il tubo.