Mai sottovalutare l’incisività di un video nella promozione aziendale, specialmente quando si dispone di una fabbrica che sembra l’officina stessa del Dio Efesto, che arrossò la cima vulcanica dell’Etna nelle notti di lavoro ininterrotto per intere generazioni. Un colpo dopo l’altro, oppure… Sotto la pressione incalcolabile di una possente volontà manifesta. Perché plasmare il metallo non deve per forza richiedere, in maniera inerente, l’applicazione momentanea e ripetuta di una serie d’impatti, scaturiti dalla forza cinetica di un maglio. Quando risultati altrettanto validi possono essere ottenuti, per così dire, con le buone ovvero grazie all’uso del tocco “leggero” di una cara macchina, capace di veicolare una pressione pari o superiore alle 3.000 tonnellate per centimetro quadrato. Appena sufficiente per poter comprimere qualsiasi agglomerato d’atomi, inteso come il reticolo cristallino dell’acciaio riscaldato al calor arancione-rossastro (circa 870 gradi) così da essere perfettamente malleabile, morbido e cedevole dinnanzi al desiderio implicito di raggiungere uno Scopo finale. Ma indurre i semi della trasformazione a germogliare, ricercando il frutto originariamente richiesto dall’ignoto committente, non è sempre facile e per questo la sequenza, accompagnata in questo caso unicamente dai soli effetti sonori, senza musica o commenti fuori luogo, finisce per estendersi oltre i 12 minuti complessivi, offrendo una finestra siderurgica verso una delle industrie più spettacolari ed infuocate dei nostri giorni.
Un passo dopo l’altro, a partire dall’estrazione del billetto (blocco di metallo) ortogonale dalle profondità di una gigantesca fornace, che scopriamo presto appartenere alla compagnia tedesca di Remscheid, Dirostahl, grazie all’impiego di quella che può essere soltanto definita come una grande pinza motorizzata, simile a un muletto fuoriuscito dalla cinematografia della serie Terminator. Il cui passaggio, fino alla matrice di compressione, viene doverosamente seguito dalle telecamere, mentre il fluido che alimenta i macchinari si concentra nei condotti sovrastanti al macchinario principale dell’intera operazione. Ed è all’arrivo di un segnale del tutto inaudibile, sopra il frastuono dei motori e gli ingranaggi, che la cosa attentamente surriscaldata inizia ad essere premuta e poi girata, premuta e poi girata per un certo numero di volte. Ciascuna corrispondente alla creazione di una singola sfaccettatura del componente desiderato, che nel contempo continua imprescindibilmente ad allungarsi. È questo l’effettivo inizio, un colpo alla volta, di un procedimento in cui le tolleranze sono minime, così come le occasioni di distrarsi dall’esecuzione di un copione ben collaudato. Perché non è di sicuro facile creare un pezzo del peso di almeno 35 tonnellate, che dovrà ruotare vorticosamente a circa 250 giri al minuto…
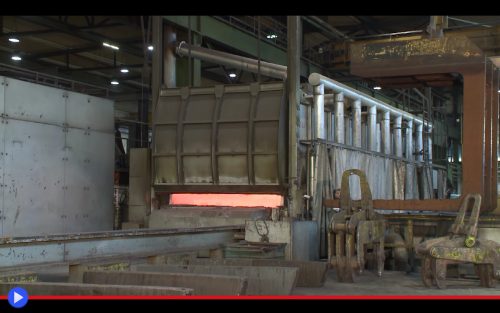
Operativa da un periodo di 400 anni nella Renania Settentrionale-Vestfalia, in base al breve trafiletto della storia aziendale offerta sul sito di riferimento, la Dirostahl realizzava originariamente coltelli e attrezzi agricoli grazie all’energia idroelettrica del suo mulino alimentato a energia idroelettrica. Abbastanza da costituire una significativa eredità familiare, capace di collocarla oggi nella cerchia dei migliori fornitori di servizi siderurgici del suo affollato ambiente di riferimento. E sebbene gli stereotipi nazionali non debbano né possano ogni volta rivelarsi corretti, sarebbe difficile non notare nella precisione dei passaggi e l’esauriente catalogo di questi video promozionali quell’attenzione ai dettagli che per tanto tempo è stata associata a un certo tipo d’industria tipicamente tedesca, dove semplicemente nulla viene lasciato al caso. Mentre progressivamente, la cosa più simile all’albero maestro esistente nel campo della marina contemporanea viene fatto avanzare nello stampo, affinché un preciso sistema di controllo numerico si occupi di misurare le appropriate differenze nel diametro ai diversi punti del componente. Senza che quest’ultimo sembri, in modo alquanto strano e sorprendente, raffreddarsi e perdere per questo la malleabilità, forse grazie a una o più sessioni di riscaldamento intermedio che non vengono mostrate all’interno della sequenza. Forse proprio perché si tratta di un montaggio, realizzato dall’utente FuTek BBM sulla base delle immagini reperibili anche sulla pagina della compagnia, con la riuscita finalità di ripristinare (o simulare?) l’audio originale di ciascun momento. Il tipo tuttavia di operazione che difficilmente può riuscire a risultare inviso ai produttori originali delle immagini, quando si considerano gli otto milioni e mezzo di visualizzazioni a partire dal marzo scorso, ovvero molte dozzine di volte quelli ottenibili grazie alla pubblicazione presso un semplice canale di YouTube aziendale. Alla fine del processo, quindi, il pezzo ormai freddo viene attentamente levigato al tornio mentre grandi trucioli si avvolgono su loro stessi. L’oggetto già risulta straordinariamente lucido e riflettente.
Ed è facile comprendere grazie a tali immagini, in maniera collaterale all’intento promozionale di partenza, l’effettiva serie di vantaggi offerti dal processo di forgiatura realizzato con stampo aperto, durante il quale il “guscio” esterno del materiale viene progressivamente rimosso mediante la formazione del cosiddetto scale o scarto, indotto a staccarsi progressivamente e raccolto come prodotto collaterale, mentre il nucleo del materiale mantiene il calore vedendosi plasmato nella modalità indotta dal meccanismo di compressione dell’officina. Un approccio che riduce l’eventualità della formazione di vuoti, migliora la microstruttura e con essa la qualità interna, aumenta la resistenza agli urti ed alle sollecitazioni del componente. Il tutto mantenendo un costo complessivo nella maggior parte delle circostanze inferiore, e non di poco, a qualsivoglia tecnica di fusione veicolata al fine di raggiungere risultati della stessa natura. E chi può dire quando cognizioni simili, un giorno, potranno dimostrarsi effettivamente utili nel corso della nostra vita?
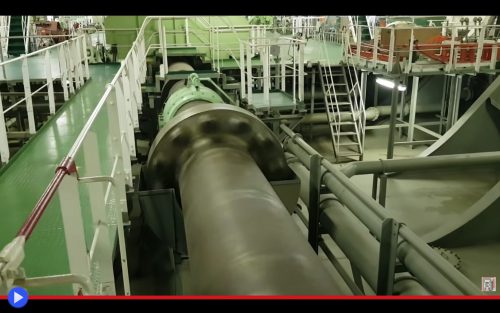
Ogni opera complessa, di per se stessa, possiede le caratteristiche necessarie a renderla interessante. Non è d’altronde facile trovare qualcosa di maggiormente affascinante per la mente umana, che il fuoco stesso dell’industria, veicolato con le metodologie più dettagliate offerte dalla scienza e la tecnologia moderne. Proprio per questo, anche se è probabile che i nostri transatlantici presenti e futuri vengano già forniti completi di un albero di trasmissione, è utile vedere le caratteristiche all’origine di un tale approccio alla meccanica sovradimensionata. Poiché la cognizione dei princìpi di massima aiuta a motivare ogni tipologia di scelta, critica, logica o situazionale. Anche al di fuori di quel singolo, spettacolare contesto di riferimento.